Ameren Missouri
This year’s Fortnightly Foremost Innovator in virtual reality, the team of Daniel Benke, Juan Cortez, Arron Pauley, and Lorne Poindexter at Ameren Missouri enabled workers at the Callaway nuclear plant to recognize hazards and are now constructing a three-dimensional model of the plant for teaching safe procedures.
PUF's Steve Mitnick: You've created this amazing virtual platform, which sounds so useful for the Callaway Plant. What does it do?
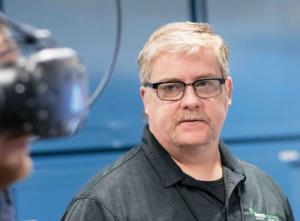
Arron Pauley: In 2019, we had a bottleneck when it came to trying to get throughput in our training. We have a flow simulator we would use to do training with our lock out, tag out.
We call it Workman's Protection Assurance or WPA at Callaway. You take them in and walk the tags down. Can they verify they're looking at the right location, the right tags and their WPA is correct? With throughput, you can only get about ten people in the physical lab at a time.
We started thinking about different ways to do that. We've been looking at virtual reality and the different platforms, and how can we build a virtual WPA or lockout/tagout walk-down?
We worked with the vendor, took our current training, and replicated our classroom into a virtual space. We did the pilot with workers at the site. Then, we developed it for training for our contractors. We were able to take more people and put them into a virtual room.
Instead of them actually putting their gloves and hard hat on, we strap on the goggles and the headset, and we walk into the room just like we are there. We have our posters on the wall, and all of our documentation.
We go into the room, and then we get to walk it down. We get to look at the WPA, and look at our tags, make sure we're working at the right location, using all our human performance tools, and three-way communication, then stopping and taking a break.
All of what we would do if we were in the plant, we can do right there in the virtual space. As an instructor, I can sit and watch everybody because I can see what they are looking at, and I can ask my directing questions. I can make sure to reinforce what's going on.
The workers loved it. They were engaged. They were seeking me out. I had workers who were in the hallway wanting to know how they could go to the class.
For this refuel, we put together a virtual reality training for hazard recognition. I had some of my same students from the WPA training, and as soon as they saw their schedule, they said, we get to do virtual reality again.
They were excited about the same type of experience again, going into the virtual space. You walk around in this area that we create, and that's the nice aspect about the VR experience. No matter what we're doing, we can create any type of environment. The software is easy to use.
We can take our 3D drawings, CAD drawings, SolidWorks drawings, any types of these drawings that we want to model and drop them right in to create any type of environment. You can drop PowerPoints and videos into it and have this completely interactive environment.
It's fun to watch the students get absorbed and focused in on what they're doing. That way, you know they're listening and taking notes. It's amazing to watch the students, because a lot of people don't have VR experience. They don't have this at home, so when they're coming to the workspace they get to step into that other world.
It's kind of like the movie, Ready Player One. It's like taking them into the OASIS. It's fun to see some of them. They had so much fun learning in it.
With the training, we can let them do all of our objectives, make sure they understand their tagging, and then I let them play. We could do place-keeping playscaping, so they can mark on the paper copy on the wall. I duplicate and have another room. I don't have to worry about the model getting messed up, so these workers get to engage in and understand what virtual reality can do for them.
PUF: Is it realistic?
Arron Pauley: Yes, it's to scale. If I put a standard valve in the room and it's to scale, when you walk in there, you're looking at the valve just like it looks in the plant. If there's something on the floor, you kneel down right there and look down on the floor, and everything is in the same spatial relationship it would be in a real room.
We take a minute or two and show people how the headsets work. I give them the controller to take control. I show them the basic controls for moving around, picking items up, or pointing at things, or drawing, and then we go into the room.
The way the software works, it can set up a little parameter, so that way it can keep you in your own little space. A little grid wall pops up, so that way you can make sure you're not moving outside your space. I had ten people, all in the same room at the same time, looking around, and writing stuff down. You see all the little avatars in the room, so everyone's in the same place.
We could even set up a digital meeting and I could take you through it, using the computer. I could teach you from a distance. That's what we're doing now with our hazard recognition. We're having on-line meetings and taking people into the room to do this type of walk-down and early recognition.
PUF: This seems to have other benefits, too, as far as safety. You could set up certain situations.
Arron Pauley: Yes. That's what's feeding into our next project. We're doing scanning of the site. This can help reduce radiation exposure too, as I can take you into that type of room, and we don't have to worry about dose rates.
We can do virtual walk-downs to the area. Now you can bring the student into the room. It's a 3D model, and we can move around and have an open discussion. Before we even go out to the field to do our work, we've physically been there, but it's in virtual space.
PUF: Was this easy to set up?
Arron Pauley: It's 3D models. The plant's got models made in SolidWorks or just standard CAD models. I make my own 3D models, and I can drop those right into the room. I can scale them as big as I want.
I've got a valve in one room, and we wanted to see the internal workings. With the software, I can turn around and say, you're not metal anymore. Now you're glass. You can see the inside of the valve.
You can change the properties of the item so you can see internal items that you wouldn't be able to see from an X-ray vision. It's really neat. With the different items you can manipulate the properties of it, and it's easy. You drop it in, click, and drag.
If you want a PowerPoint in it, you take the same PowerPoint, drop it in, and it creates this bulletin board. Now your PowerPoint's in there. Or if you want a video, you drop the video in and then, you're in the world. You walk up and play the video, and all of a sudden, you sit there and watch the video inside the virtual world.
PUF: How did you come up with this?
Arron Pauley: I started at Callaway in 2008, as an instrument and control technician. Loren Poindexter, senior manager nuclear and fossil innovation, was one of my managers.
Since I'm the nerd in the room, of course I'm the one with all the neat toys. We were doing all kinds of stuff and Loren was bouncing things off of me, like, I want this. I'm always tinkering with things. We played off each other, and then when Loren moved to the innovation group, he got to see some of the work out there, so he said, what do you think?
I have a theater background, too. I've been designing and building sets since the beginning of high school. Now I have this personal space where I can create anything I want. From theater, I was thinking, this is just building a big set. What do I want to do?
With my CAD background it started taking off. Loren, being part of innovation and being at Callaway in the past, knew that our WPA was always a bottleneck for our in-processing.
We thought, we could do this, and we started putting it together. I've talked to INPO. I've shown them demonstrations. We've done demonstrations for EPRI.
In the VR training, I can bring you in the room and take you through the training, so if you were coming to Callaway to do something, I could take you in the virtual space and get your training done before you even get on site. That's what we're doing now with our hazard recognition, where people are still working from home. Our senior management staff are coming in and they're delivering the content to them. They're doing it all through the Team's application.
PUF: What's the potential here, a few years out?
Arron Pauley: We've got a 3D scanner and we're doing LiDAR scans of different area. With Ameren, they've been working on their switchyards. With some of the switchyards that are all over the state, we're getting them scanned. Instead of those workers having to drive two hours to look at a location, we can bring up the scans, take it, and do the same thing. They can virtually walk the switchyard two hundred miles away.
We can build these places that people can go to without physically being there, then they're more prepared for the task. Any of our groups can then also see what they may need at the location. When they get to the location, they have the tools they need.
PUF: With the emphasis on safety, it seems like the potential could cross the industry.
Arron Pauley: That was a positive, like with engineering. We've been scanning and modeling things, so all the groups can come together. We can drop it into the VR space, and everybody can look around.
You can have that virtual meeting. You have a Microsoft Teams meeting where you see each other, or you can see a PowerPoint. This is a virtual Teams meeting, where, if you have the headset or equipment at your location, you can put it on and step in there, and now you can walk around the components. You can point things out.
Everyone's got an avatar, and you can see what you're looking at, so you can have conversation. You can make annotations, like, we're looking at this big diesel generator, and everybody can make notes of, wait, this piping might be in the way. Let's think about what we might need to do to move this out of the way.
All of that's captured in that VR space, so it's just an empty room that you can drop any type of model in, and everybody can look at it.
Profiles in Innovation
- Arron Pauley, Ameren Missouri
- Girija Sathyamurthy, Ameren
- Zachary Wassenberg, Burns & McDonnell
- Geoff Blanford, EPRI
- Maria Guimaraes Biagini, EPRI
- Anil Kondabathini, HyoJong Lee, Reynaldo Nuqui, and Jiuping Pan, Hitachi ABB Power Grids
- Dave Geier and Stephen Johnston, San Diego Gas & Electric
- Alyssa Grigoryan, Kathy Hidalgo, Sunanda Singh, and Lucero Vargas, Southern California Edison